Replacing worn engine valves is generally quite difficult, tedious, and expensive. The complexity of valve replacement jobs depends primarily on engine design, valve condition, tool availability, and mechanic skill level. Pushrod engine designs allow easier valve access versus more challenging overhead cam layouts. Sticking valves require simpler servicing than bent or broken parts.
Specialty tools and professional expertise are often needed for valve machining and proper installation. The process involves partial engine disassembly, cylinder head removal, valve spring and keeper removal, potential valve refacing, and careful reassembly. So, valve replacement can take many hours and cost several hundred to thousands of dollars in parts and labor.
This article explores the key factors affecting valve replacement difficulty, the experience required, job length, in-frame service options, and overall repair costs.
Is it hard to replace engine valves?
Yes, replacing engine valves can be quite difficult and labor intensive depending on the specific engine design, extent of valve damage, availability of proper tools, and mechanic skill level. While an experienced mechanic can handle a valve job on simpler engine designs, overhead cam engines often require professional service and machine work.
Factors influencing the complexity of valve replacement
The difficulty of replacing engine valves depends on several key factors:
- Engine type and design. Overhead cam engines with the camshaft(s) and valves located in the cylinder head require more labor-intensive disassembly to access the valves. Older pushrod V8 engines with the cam in the block have easier external access to the valve train. The number of valves – two per cylinder or more in multi-valve designs – also affects complexity.
- Extent of valve damage. Sticking valves that need refacing and seat recutting are easier than bent, burnt or broken valves requiring complete replacement. Built-up carbon deposits increase cleaning work.
- Availability of tools and expertise. Specialty tools like valve spring compressors, cylinder leakdown testers, and machining equipment for valve refacing are needed. An experienced mechanic familiar with the specific engine is important.
Skill level required for valve replacement
- DIY approach for experienced mechanics. Hobbyists who are skilled with engine rebuilding can replace valves on classic pushrod V8s or older 4-cylinder engines. But overhead cam engines require more specialized experience.
- Professional assistance for novice mechanics. Less experienced shadetree mechanics should have valve work done by a professional shop with the proper tools and expertise. Paying a machine shop for valve refacing is advised.
How long does it take to replace engine valves?
The time required to replace engine valves can range from 2 hours for a simple 4-cylinder engine to 8 hours or more for a complex V8. The engine must be partially disassembled to remove the cylinder head and access the valves. Each valve’s springs, keepers, seals and guides need to be removed and replaced. Valves may need refacing and seat recutting. Reassembly with proper adjustments takes time.
Can you replace engine valves without removing the engine?
On most modern engines, the cylinder head must be removed to access the valves, requiring the removal of intake, exhaust, accessory drive belts, and exhaust manifold(s). So in-frame valve replacement typically isn’t possible. However, some older V8s allow keeping the engine in the vehicle when replacing valves.
Is replacing valves expensive?
Valve replacement costs vary depending on labor rates, parts, and machine work. As a rough estimate, expect to pay $400-800 or more for a basic 4-cylinder engine valve job. For an overhead cam V6 or V8 engine, valve replacement can easily cost $1000-2000+ with labor and parts. So it’s a significant repair job.
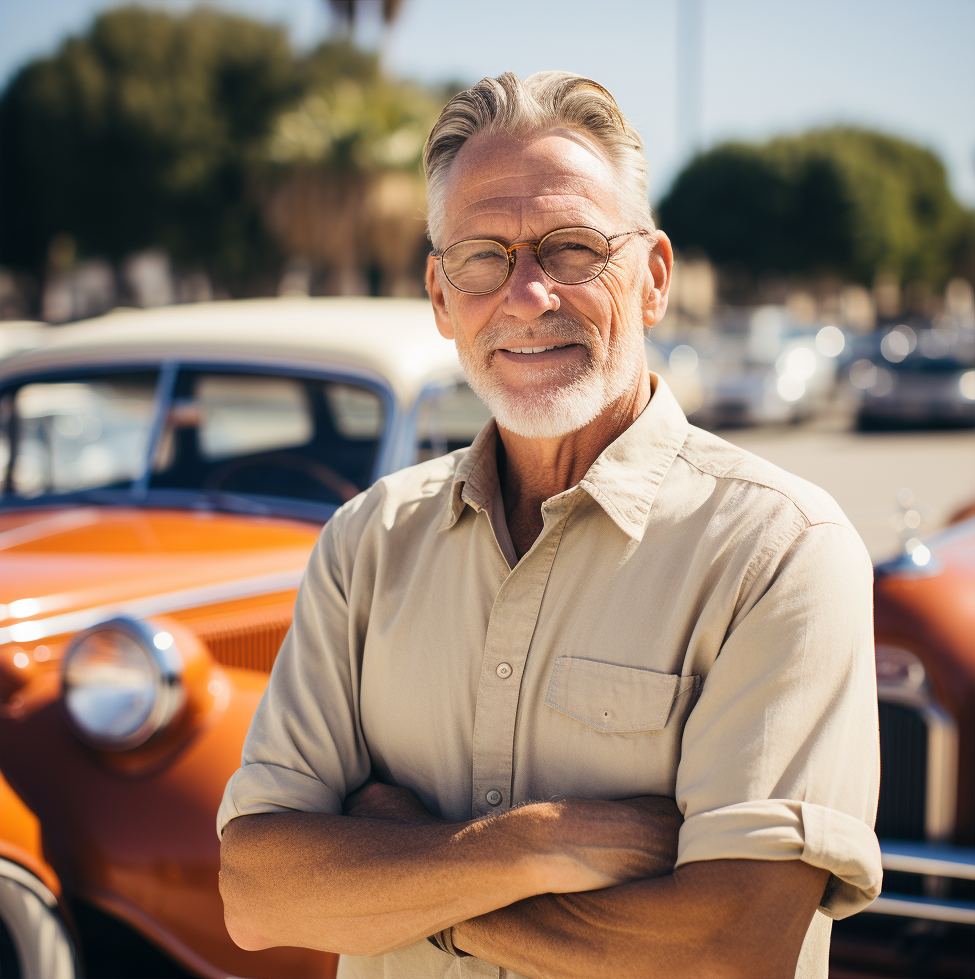
John Smith, a Los Angeles-based car specialist and automotive writer, boasts over 20 years in the industry. With a background as a master technician and a decade-long writing stint at notable automotive publications, John now shares his expansive knowledge on CarFinite, simplifying car maintenance for readers.